Argon 18's Focus on Performance
Our Performance Protocol
Argon 18 bikes are known for their ride quality, contemporary design, and high performance – for top pros, local circuit champions, and everyday riders alike. We use a rigorous process of design, engineering, testing, refining, and validating, and apply leading technologies and tools to prioritise premium performance and rider safety. Go behind the scenes at Argon 18 to learn more about what sets our bikes apart.
Carbon Engineering
Like most high-performance bikes, Argon 18 bikes are made from carbon fibre composite. Both performance and safety characteristics of our bikes are determined by the structural characteristics of carbon fibre, and by the precise benchmarking, testing and simulation modeling as part of the structural engineering process. Joffrey Renaud, Lead Composites Engineer, and Pierre Legay, Structural and CFD Analyst, take us behind the scenes to understand a core part of our process.
What are the characteristics of carbon fibre composite?
All “carbon” bikes are actually made of a composite: a mix of carbon fibres in a matrix of epoxy resin. Carbon fibres are bundled into thin layers, or plies, within this epoxy matrix. Carbon fibers are used for their high stiffness and strength along the fiber direction, and for their low density.
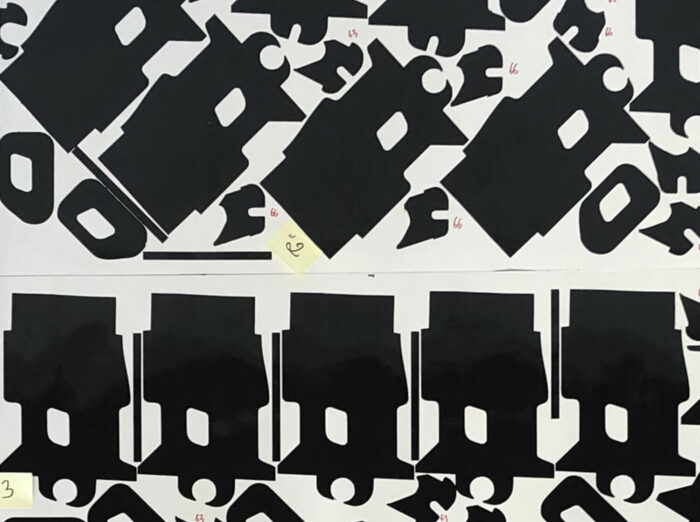
How does layup affect our lineup?
Our lineup features three levels of performance in most categories: Pro, Elite and Cyclosportif. Each of these levels has requirements when it comes to the choice of carbon layup, and each bike category also has unique characteristics. An Elite level gravel bike demands a different layup than an Elite triathlon or road race bike, for example. Even though we have three levels of carbon layups that match our levels of performance, the way we use them will differ from one frame to another in each of our model segments.
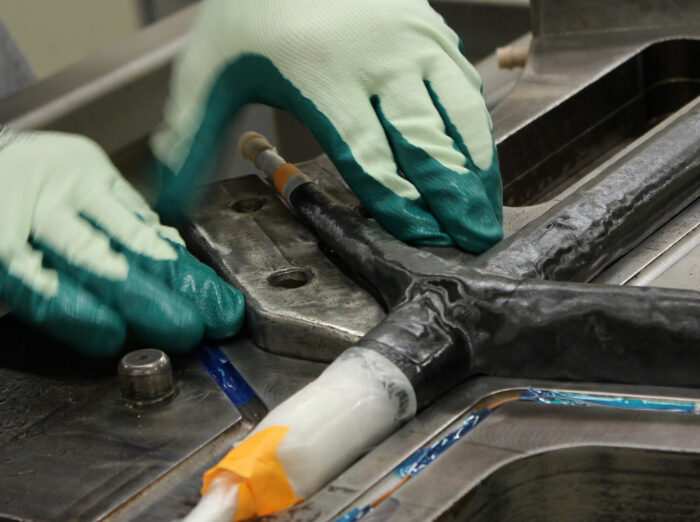
Our work at the CDCQ
Argon 18 is collaborating with the Composites Development Centre of Quebec (CDCQ) to refine our fabrication processes and expand our hands-on knowledge of carbon engineering and manufacturing. This project involves the production of prototype frames, with our R&D team involved in the process from start to finish: creating the layup, designing all the tools required for fabrication, such as mandrels and layup jigs, laying the plies, testing and validating the resulting frames.
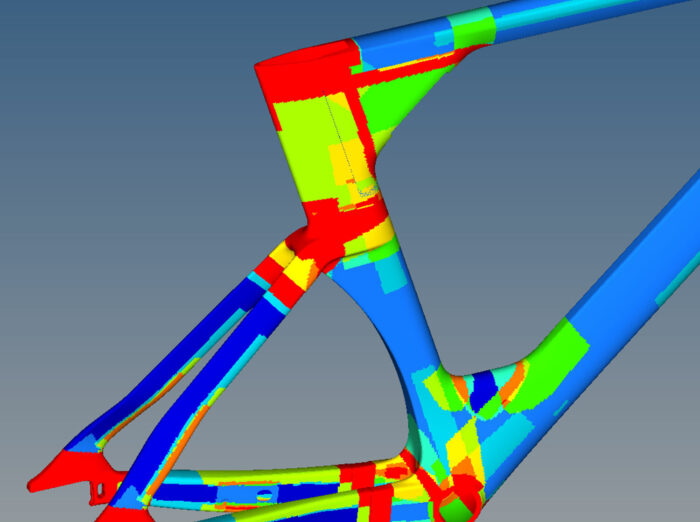
What do we mean by layup optimization?
An optimized design solution provides the best possible result when a constraint is placed on a set of variables. For example, the variables in frame design include the number and orientation of plies in a layup, the materials, and the tube shapes. The constraints come from the specific benchmarks that we want to achieve with the bike, such as specific stiffness targets and strength.
Aerodynamics
Aero is often seen as the holy grail of cycling: aerodynamic performance influences everything from clothing to components to positioning, and of course the design of the bike itself. What are the main principles of aerodynamics, and how do we address them in our bike design?
Aero Drag: the Basics
There are four major contributors to rider displacement: air resistance, altitude gain resistance, acceleration resistance and mechanical loss. The ratio of the contribution of these four forces changes based on riding conditions. Altitude gain resistance increases as the grade of a climb increases, for example, and air resistance decreases on that same climb as the rider slows down.
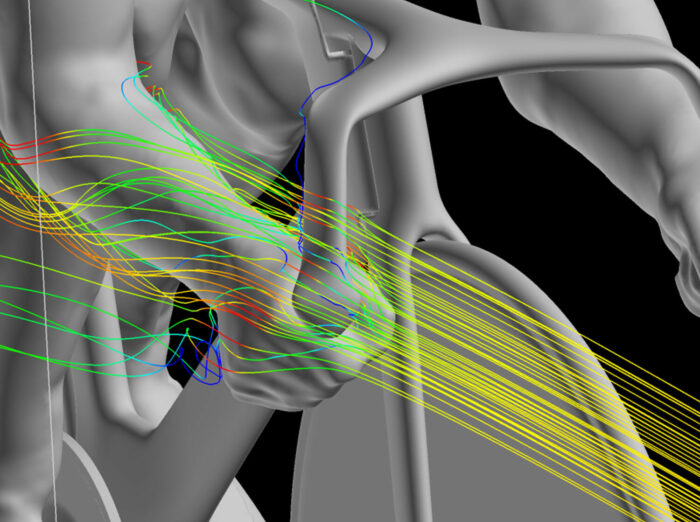
Computational Fluid Dynamics
CFD is a numerical simulation tool to predict aerodynamic performance. You’ve probably heard of CFD being referred to as a “virtual wind tunnel”, but both CFD and the wind tunnel have their own unique role in the development process. In CFD, we can see how the flow of air - the "fluid" in CFD - behaves around rider and bike frame. This analysis can lead to design changes that improve the flow around fork and frame shapes.
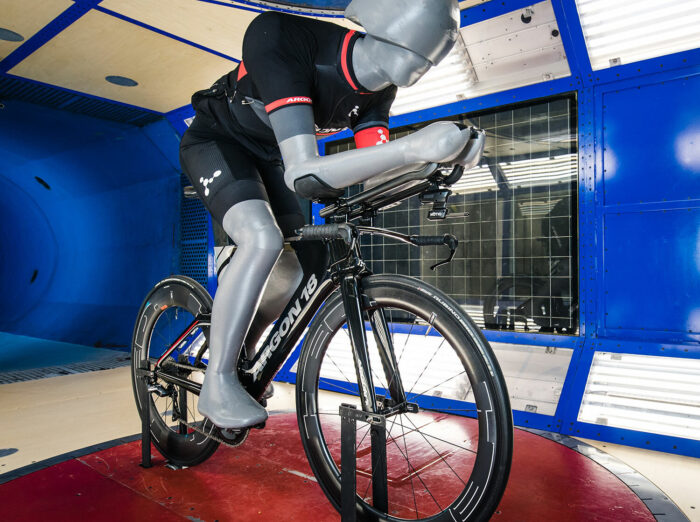
Testing in the Wind Tunnel
There are two parameters we can address to improve the aerodynamic performance of an object: its shape and its frontal area. We can see the effects of adjustments to both of these parameters by measuring the CdA, or drag coefficient. In the wind tunnel, a controlled air flow with known velocity is applied to the rider. Load sensors are used to measure the force applied by the air on the rider, and yaw angles are carefully weighted to reflect real-world conditions.
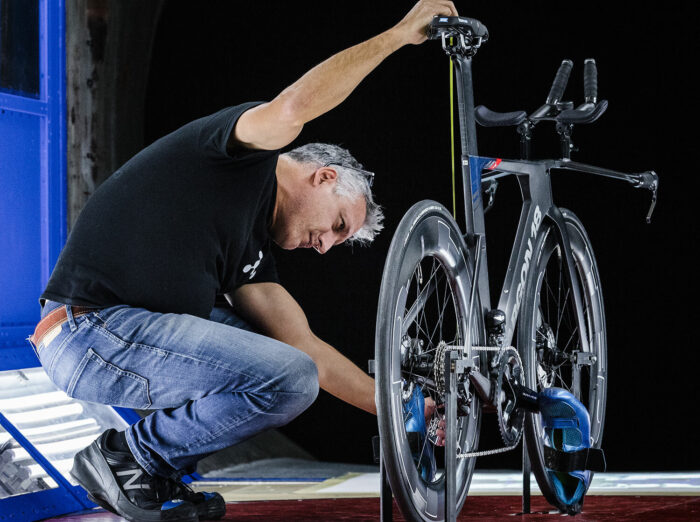
How does aero testing affect our design process?
Aero performance is one of the key features of our bikes, and is repeatedly measured and evaluated throughout the development process. However, aero is always analysed in conjunction with how new shapes affect stiffness and weight targets. All parameters are evaluated simultaneously, in a holistic approach. We evaluate initial design concepts this way so that we can be efficient in producing design iterations that move us closer to our performance goals across all parameters.
Prototyping
Prototyping is a key stage of our development process where we produce a physical model to validate or further investigate our design intentions. We use prototyping as part of two key processes: our bike development, and our advanced research projects.
There are several major reasons why we produce prototypes as part of bike development:
- To test real-world functionality: we test the performance of design features such as integrated cables or component compatibility, or to be sure the bike’s assembly will be mechanic-friendly.
- To continue performance testing, such as the wind tunnel testing described in our article on aerodynamics, which is often undertaken with a prototype.
- To undertake safety testing.
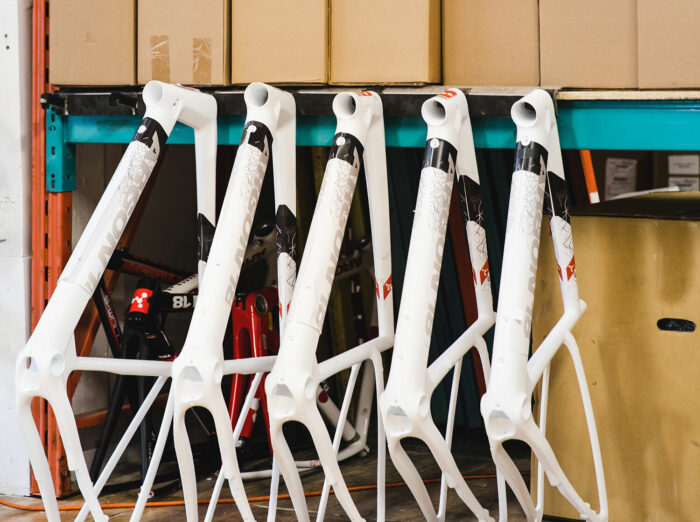
Prototyping as Part of Design Validation
Early looking samples allows us to check the quality of the mould. We will be able to see if the surfaces of the frame are smooth, the tube shapes are accurate, and if the fit with required plastic parts is compatible. We are also able to test artwork at this point, to be sure the final product will be produced true to the design intentions.
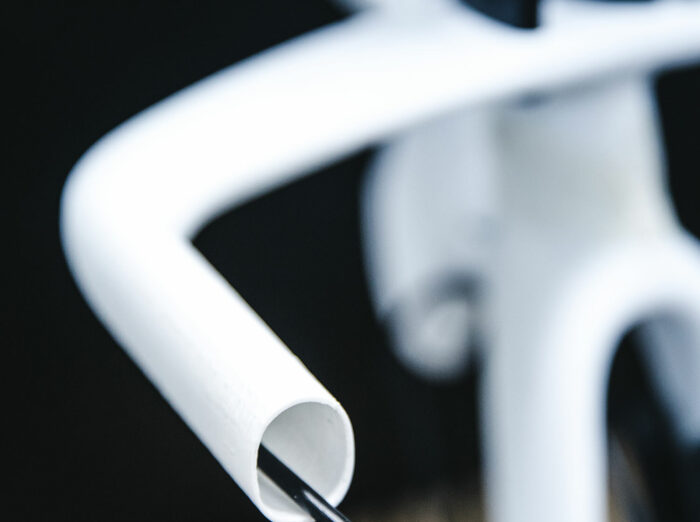
Prototyping as Part of Advanced Research
We often use prototyping as part of our ongoing advanced research programs. In this research we may not be working on one specific model, but rather looking to gain new knowledge on the behaviour of certain areas of the bike frame, or further develop our expertise in composite engineering.
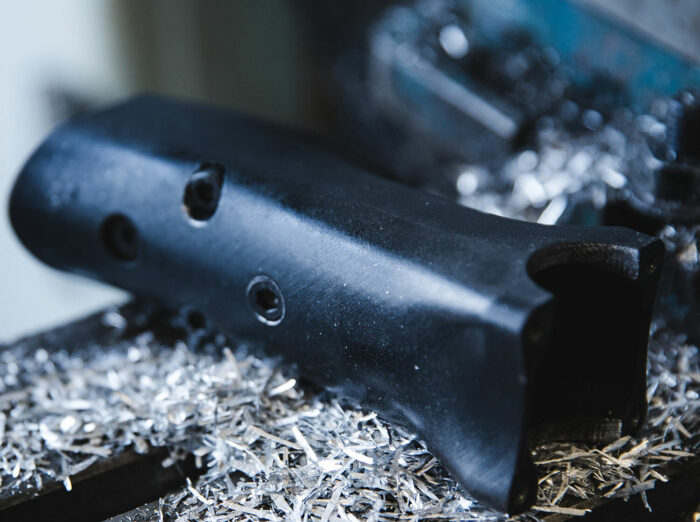
The Link to Manufacturing
The expertise we develop with our prototyping techniques means we are able to propose new methods to our partners in our manufacturing facilities based on our own hands-on experience with the techniques of production. This makes our working relationships more efficient, and adds a level of collaboration that helps us provide the best possible products to our riders.
Testing
The safety and performance quality of our bikes is our largest priority. Our testing and quality control protocols are among the most rigorous in the industry, and we are constantly adding to or augmenting our test standards to ensure the best possible experience for our riders.
Overall, our testing falls into two main categories: performance requirements and safety requirements. Safety requirements are industry-wide standards. Performance requirements include assessing the benchmarks we set for each bike, such as weight, comfort, handling, stiffness, and aerodynamics, among other performance benchmarks.
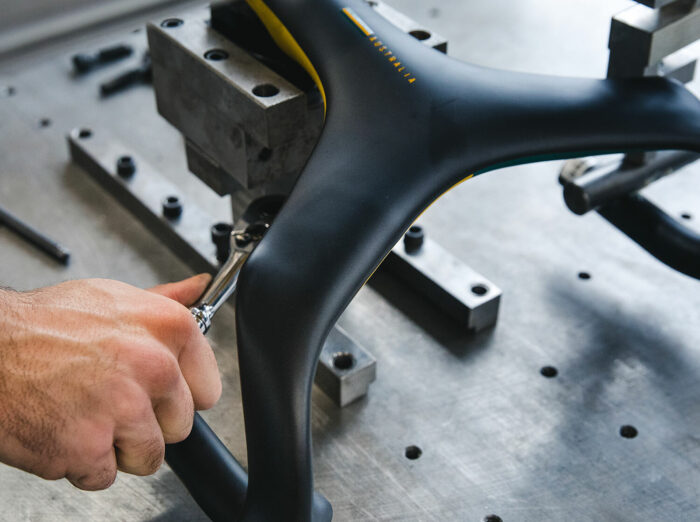
Safety Tests
Safety requirements are industry-wide standards. Often these are set by ISO guidelines (International Organization for Standardization), although we have developed and implemented additional tests where we feel appropriate.
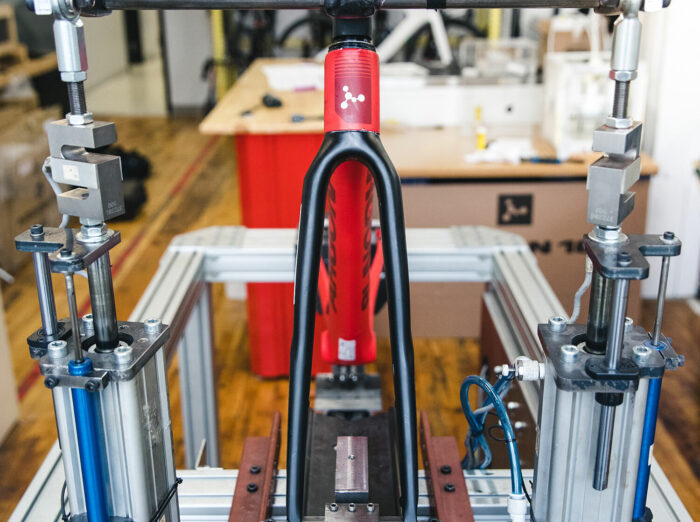
Testing Protocols
Safety tests take several forms to be sure we test all possible parameters and meet all international safety standards. In static tests, a load is applied to the frame and maintained during a short time. In fatigue tests, a load is applied under repetitive movement. In impact tests, a weighted striker is dropped on the frame, or the frame is dropped with weights on it.
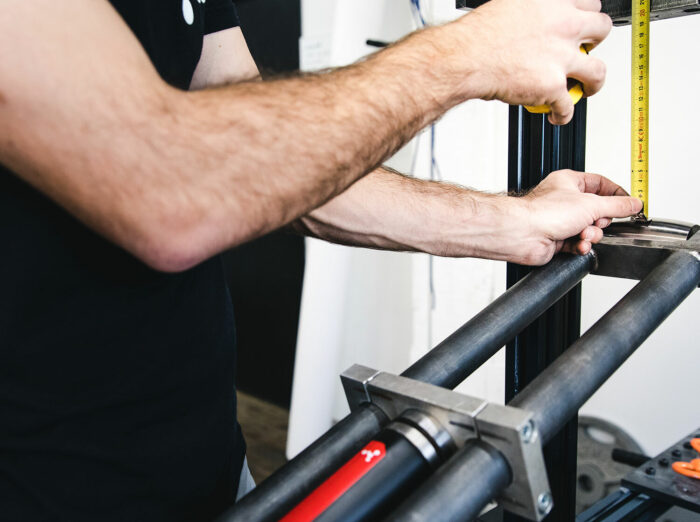
Performance requirements
Performance requirements include assessing the benchmarks we set for each bike, such as weight, comfort, handling, stiffness, and aerodynamics, among other performance benchmarks. Unlike safety tests, these tests produce discretionary results, based on targets that we have set for ourselves.
Manufacturing
The final step in our design process is manufacturing, when we enter the production phase and are able to deliver our products to our network of shops and riders around the world. Like most composite bike manufacturers, our bikes are largely manufactured in Asia. However, our team is closely involved in the manufacturing process. Our knowledge of manufacturing has been highly refined with our work with the CDCQ, which allows us to understand how production processes affect and enhance quality and performance characteristics. When we work with factories, we can provide precise information about the layup and desired ride characteristics of the bike, and know that we are working collaboratively with the production team.
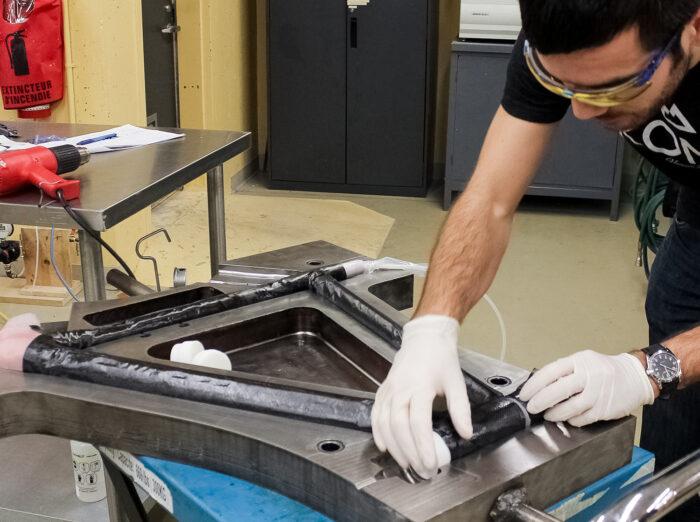
Preparing the Mould
Production processes begin with cutting pre-preg, a carbon fiber fabric that has been pre-impregnated with resin, in plies according to the layup of the particular bike. The plies are placed on a mandrel that is composed of a solid part inserted in an inflatable bladder. The mandrel is then placed in the mould. Unique moulds are made for each bike design, as well as size – each size within a model run has its own mould.
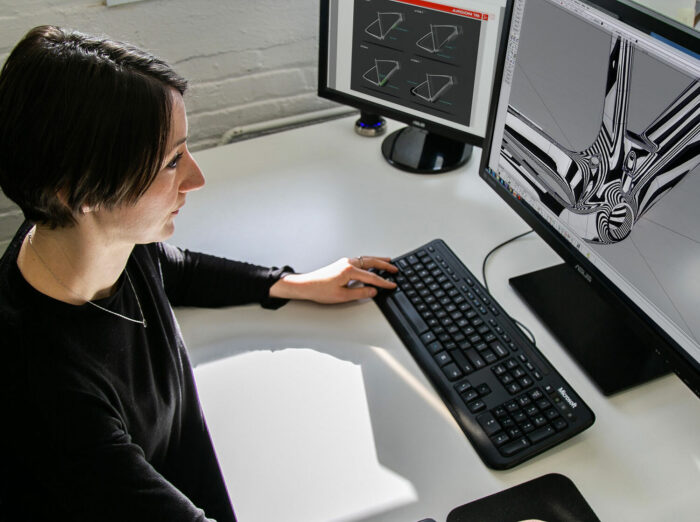
Partnerships for Quality Production
Our end-to-end involvement in manufacturing affects more than just our relationship with factories. The constraints of manufacturing influence design. Starting at square one, we design our bikes with manufacturing processes in mind, so that our designs are achievable, and so that the performance attributes we engineer into our bikes are realised in the final product.
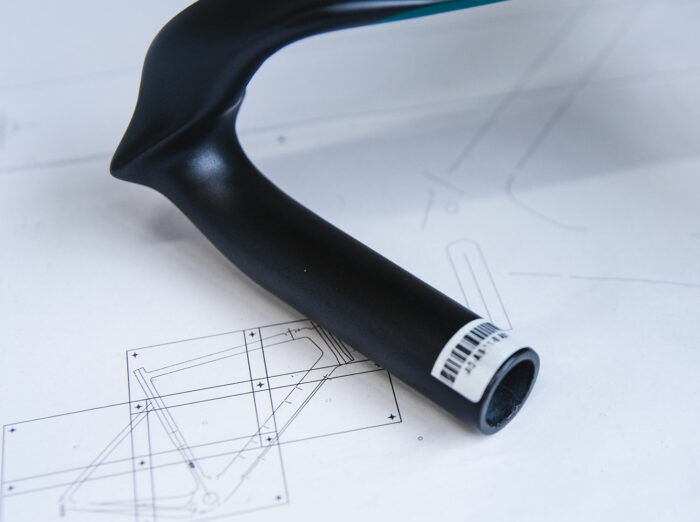
Our Holistic Approach
Argon 18’s unique products come from our unique approach to the design and production process. Design, simulation, prototyping, testing and manufacturing all work as a cycle to continually deliver the best possible performance for our riders, because we know that you’re constantly pushing yourself to perform better… and so are we.