Our Approach: Carbon Engineering
Like most high-performance bikes, Argon 18 bikes are made from carbon fibre composite. Both performance and safety characteristics of our bikes are determined by the structural characteristics of carbon fibre, and by the precise benchmarking, testing and simulation modeling as part of the structural engineering process. Joffrey Renaud, Lead Composites Engineer, and Pierre Legay, Structural and CFD Analyst, take us behind the scenes to understand a core part of our process.
What are the characteristics of carbon fibre composite?
All “carbon” bikes are actually made of a composite: a mix of carbon fibres in a matrix of epoxy resin. Carbon fibres are bundled into thin layers, or plies, within this epoxy matrix. Carbon fibers are used for their high stiffness and strength along the fiber direction, and for their low density. The resin matrix is used to holds these long, thin fibers together so that we are able to use them efficiently in product design. Different kinds of carbon fibre offer different structural characteristics, depending on how the fibres are arranged in the resin: they can be woven, mat, or unidirectional. In bikes, we usually use unidirectional carbon fibers. First of all, this pattern results in material that is lighter than mat or woven. It also gives us more freedom to place fibres of different orientations in sequence, in order to achieve precise performance criteria. For example, if we want to maximize stiffness at the bottom bracket, we’ll add composite plies with fibers oriented along the downtube. With woven or mat fibre, we wouldn’t have that same flexibility to adjust fibre angle while still being able to limit weight, as we wouldn’t be able to control the precise angles of the fibers within the resin. However, we do use woven plies near any areas of the frame which will be machined, such as water bottle mounts or cable guides, to obtain a better finish. Since unidirectional plies have more brittle properties perpendicular to the fiber direction, carbon bike parts are always made of a mix of plies with fibers placed at different orientations, so that the material is reinforced in all directions.

How do we select the type of carbon fibre we use?
Different kinds of carbon fibre have different stiffnesses, different strengths, and like all materials, different prices. Even high-end composite frames are made of different grades of carbon fibers combined according to design, performance and safety requisites. The layup is the precise arrangement of composite plies, or pieces, to make a specific bike design. It is a detailed set of instructions on the ply position, fiber orientation and type of material to be used in the manufacturing process. When you read that a new bike model has a completely new layup, that means that many characteristics of the bike have been improved due to the use of a new combination of plies of different kind of carbon fibers, orientation, or geometry. A layup is highly detailed – for example, in a lightweight racing bike, more than 120 plies are used for the front triangle alone.
How do we identify and test for specific performance indicators?
Finite Element Analysis (FEA) is a simulation tool used to predict the performance and safety characteristics of a particular layup. It allows us to calculate stresses at different points on the bike frame, and model the bike deformations under specific load cases based on the characteristics of different ply arrangements, or geometry of tube shapes. The simulations help us predict frame characteristics early in the design process and allows us to achieve very specific performance targets (weight, stiffness, strength). More than ten load cases are used in simulations of the frame, to mimic the various stresses seen on the road, such as cornering, standing and sprinting. These tests are also specific to the areas of the bike that respond to different performance requirements. There are different requirements for the performance of the headtube while riding, for example, than there are for the bottom bracket. There is also a balance required at key areas on the frame, such as that between BB stiffness and vertical stiffness. Bottom bracket stiffness is required for high performance in sprint situations, but vertical compliance is required for a higher degree of comfort. The simulation process allows us to determine exactly how to choose material, orient and position the different plies in each of these key regions. This is what gives a bike its specific handling and performance character.
Testing for both safety and performance characteristics continues throughout the design process.
What do we mean by layup optimization?
An optimized design solution provides the best possible result when a constraint is placed on a set of variables. For example, the variables in frame design include the number and orientation of plies in a layup, the materials, and the tube shapes. The constraints come from the specific benchmarks that we want to achieve with the bike, such as specific stiffness targets and strength.
For example, if our objective is to optimise the layup on a portion of the frame to achieve a weight target:
Objective: minimise weight
Variables: number, orientation, choice of material of composite plies
Constraints:
- Good BB stiffness
- Good vertical compliance
- All safety requirements
- Very high stiffness
- All safety requirements
Process: 100 to 200 analyses run
Or, to optimize the shape of a sprint handlebar on a track frame such as the Electron Pro:
Objective: minimize weight and reduce frontal area for aero performance
Variables: shape of tubes
Constraints:
Process: 50 to 100 analyses run
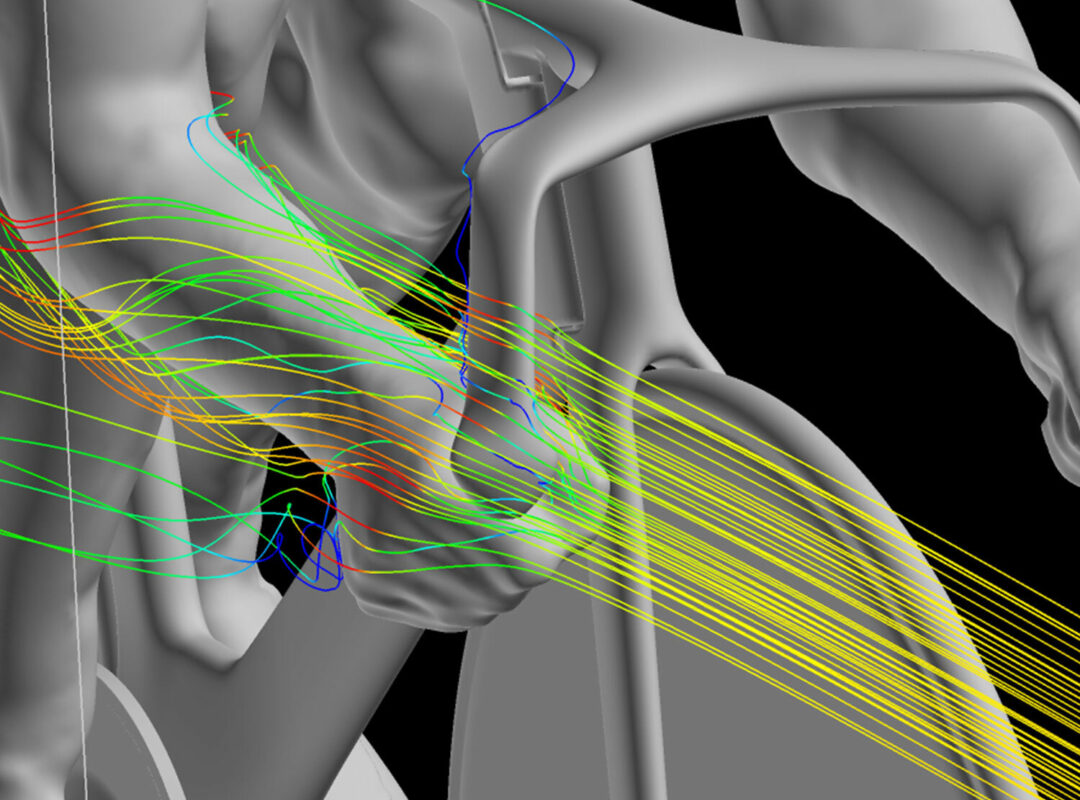
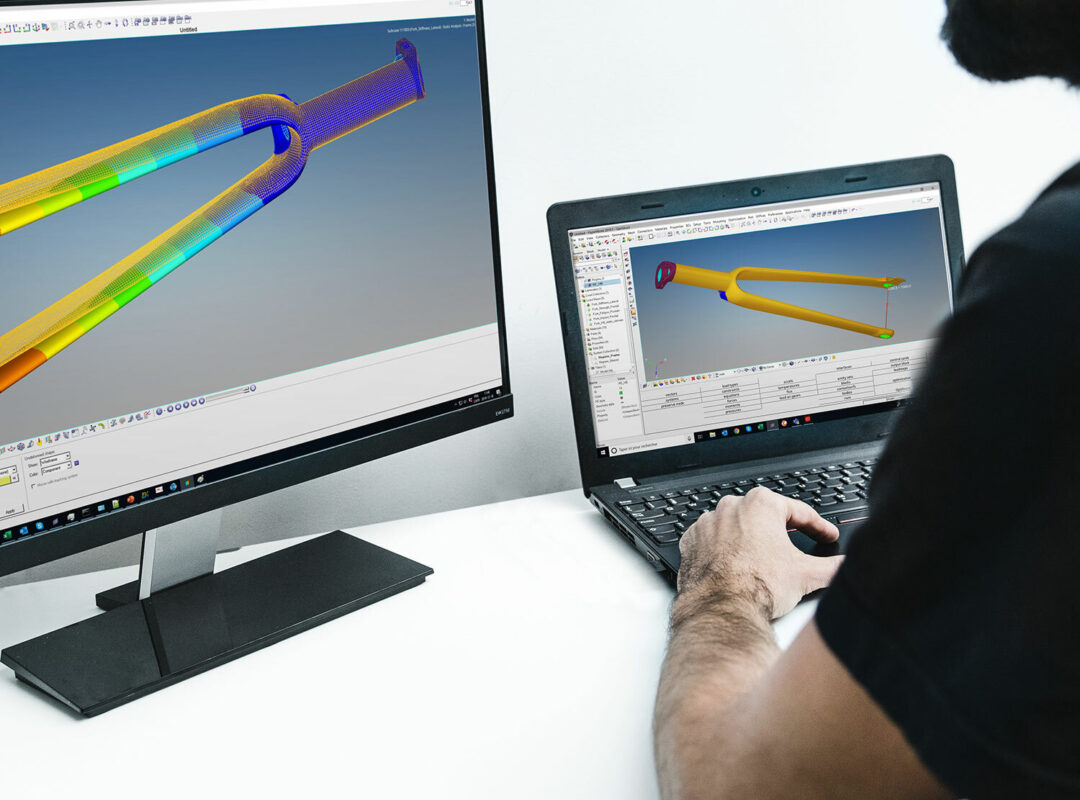
Our work at the CDCQ
Argon 18 is collaborating with the Composites Development Centre of Quebec (CDCQ) to refine our fabrication processes and expand our hands-on knowledge of carbon engineering and manufacturing. This project involves the production of prototype frames, with our R&D team involved in the process from start to finish: creating the layup, designing all the tools required for fabrication, such as mandrels and layup jigs, laying the plies, testing and validating the resulting frames.
This work has given us greater knowledge of how our design process relates to the constraints and realities of manufacturing, allowing us to refine our ply selection, layup design, and safety testing. You can read more about how this advanced composites knowledge has affected our prototyping and manufacturing processes as well.
How does carbon fibre layup affect our lineup?
Our lineup features three levels of performance in most categories: Pro, Elite and Cyclosportif. For example, in our performance road category, you’ll find the Sum Pro the Sum, and the Equation. Each of these levels has requirements when it comes to the choice of carbon layup, and each bike category also has unique characteristics. An Elite level gravel bike demands a different layup than an Elite triathlon or road race bike, for example. Our carbon layup for a Sum Pro has to match the demands and expectations of a World Tour racer who will spend long hours on the saddle every day. Our Electron Pro has to meet the stiffness demands of track riders who exert over three times the force of most standardised tests. In other words, even though we have three levels of carbon layups that match our levels of performance, the way we use them will differ from one frame to another in each of our model segments. Every model has different performance parameters based on expected use, and has to perform at the very top of its class.
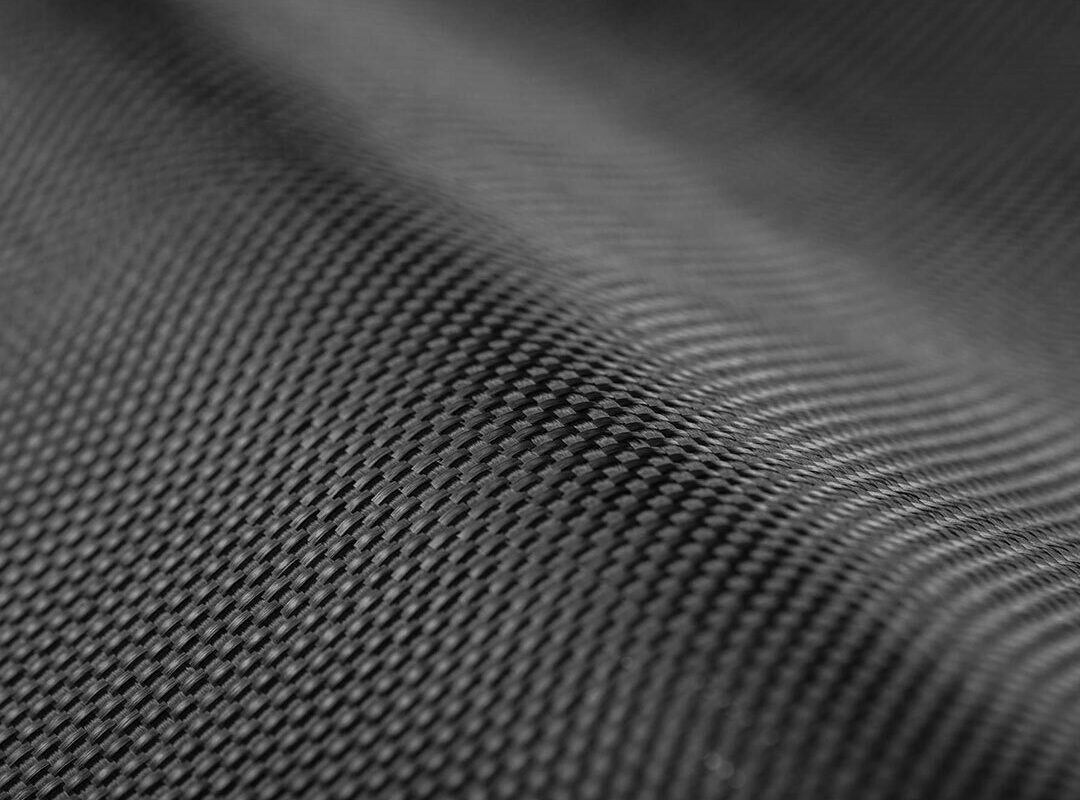
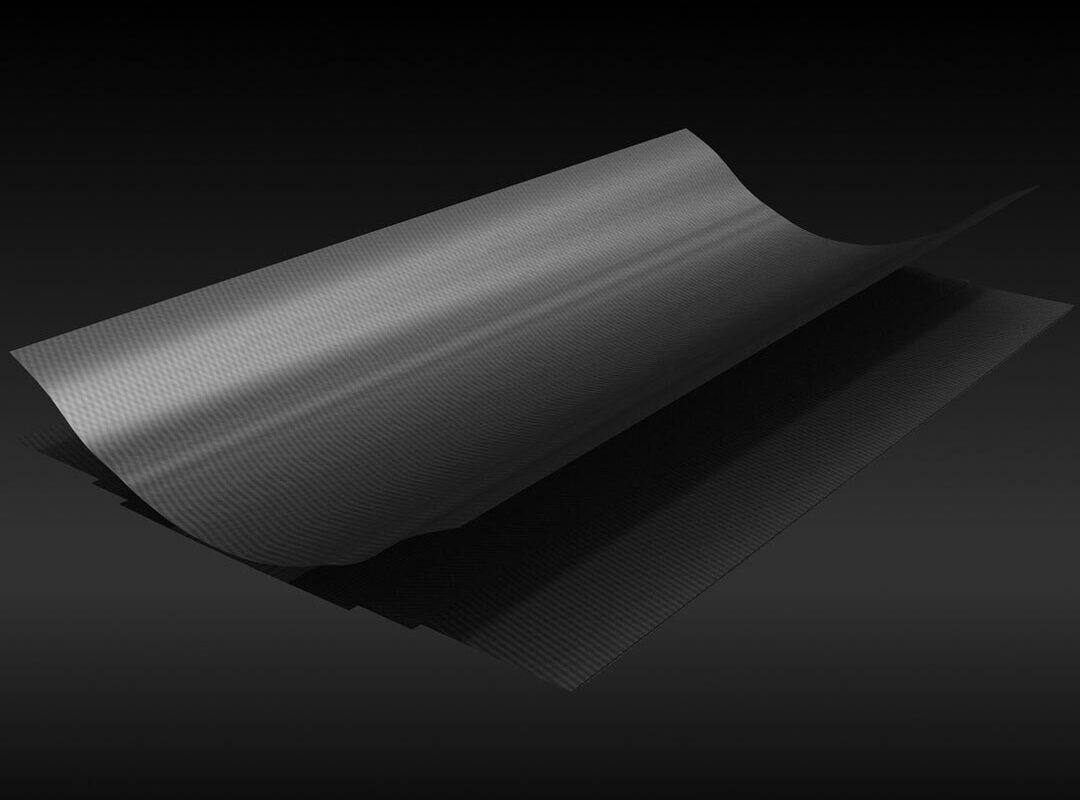
Does the grade of carbon determine the price of a bike?
A frame’s price is determined by the nature of the materials, the development time, and the complexity of the manufacturing process. Very lightweight performance bikes like the Sum Pro are made from more expensive carbon fibre composite, with more and smaller plies that require very accurate positioning. These bikes also require a significant amount of development time to optimize the layup so that the performance targets are met. However, the Equation benefits from the R&D that has already gone into the Sum Pro, which means we can offer it at a lower price. Also, since the ultimate lightweight design isn’t the top performance characteristic of the CS, the lightest and most expensive carbon fibre isn’t used to the same degree as in the Pro. The manufacturing time also has a significant effect on the frame’s price. The Pro is made of plies with complex shapes, which take significant time to layup. To reach the same stiffness and strength with lower grade fibers, the CS will use more plies with simpler shapes that are faster to lay up. This means we are able to offer a bike that has many of the same technologies and performance characteristics, but at a more accessible price point.