Our Approach: Manufacturing
The final step in our design process is manufacturing, when we enter the production phase and are able to deliver our products to our network of shops and riders around the world. Like most composite bike manufacturers, our bikes are largely manufactured in Asia. However, our team is closely involved in the manufacturing process. Our knowledge of manufacturing has been highly refined with our work with the CDCQ, which allows us to understand how production processes affect and enhance quality and performance characteristics. When we work with factories, we can provide precise information about the layup and desired ride characteristics of the bike, and know that we are working collaboratively with the production team.
Production processes begin with cutting pre-preg, a carbon fiber fabric that has been pre-impregnated with resin, in plies according to the layup of the particular bike. The plies are placed on a mandrel that is composed of a solid part inserted in an inflatable bladder. The mandrel is then placed in the mould. Unique moulds are made for each bike design, based on the desired tube shapes and geometry, as well as size – each size within a model run has its own mould. The mould is heated in order to cure the resin while the bladder is inflated, resulting in the pre-preg taking the shape of the mould. Moulds are usually made of steel or aluminum, with consistency and repeatability the main concern – there should be no deviations between frames. While the mould is formed to the shape the frame from the outside, the shape must also be formed by pressure from the inside. The inflatable bladders press the prepreg against the mould surfaces. This process of applying sufficient pressure to the inside of the frame also helps avoid air bubbles in the resin.


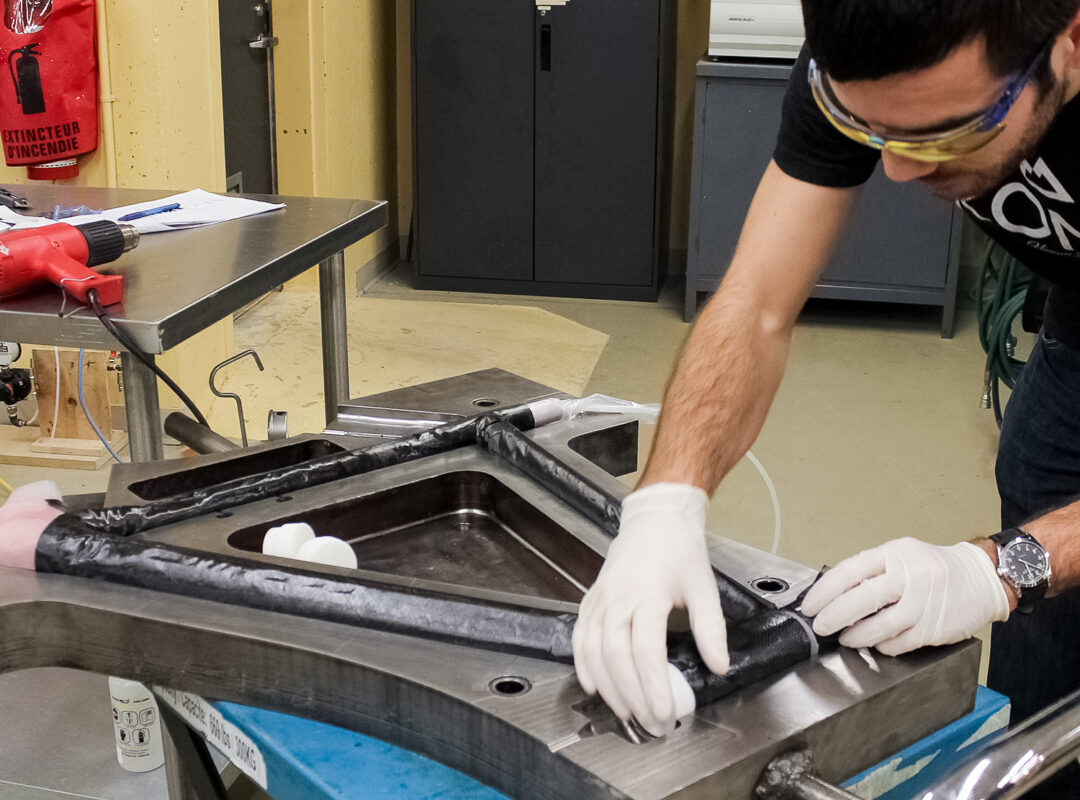
When the frame is removed from the mould, it is lightly sanded to remove any excess resin, and prepped for paint. Any required machining or drilling takes place, such as that for water bottle mounts or derailleur mounts.
While some bike companies simply send performance requirements to the factories, who then use the factory’s own layup schedules to produce the frames, Argon 18 works to be completely involved in the manufacturing process so that we are able to control materials, methods and layups. This active collaboration with the factories means we are able to push the limits of our frame design, as we understand what is really achievable at the manufacturing stage. Sometimes when we ask the factories to make changes in their standard processes we can face questions and concerns, but when we have the expertise to guide change in a focused and confident manner, they trust that we will not waste time and resources making changes that are not efficient and results-driven.

Our end-to-end involvement in manufacturing affects more than just our relationship with factories. The constraints of manufacturing influence design. Starting at square one, we design our bikes with manufacturing processes in mind, so that our designs are achievable, and so that the performance attributes we engineer into our bikes are realised in the final product. We do not design bikes that cannot be efficiently manufactured because our focus is to deliver on our promises to our riders. Our commitment to constantly improving our understanding of the performance and experience characteristics of composites engineering means we never use gimmicks or add-ons to our frames, but prefer to deliver results to our riders based on our knowledge of materials, layup and design parameters.
Argon 18’s unique products come from our unique approach to the design and production process. Design, simulation, prototyping, testing and manufacturing all work as a cycle to continually deliver the best possible performance for our riders, because we know that you’re constantly pushing yourself to perform better… and so are we.