Testing as a Team: Notio and Argon 18 Develop New Aero Testing Protocol
We’ve written before about the safety and performance testing that we put our bikes through as part of our development process (see our approach page). But just as we’re constantly developing new models, we’re also constantly refining our testing protocols on our existing models so that we can keep pushing the limits of performance and deliver the best bikes to our riders.
One of the ways we’re doing that is by working closely with the team at Notio, Argon 18’s sister company. Working together, we’ve developed an aero testing protocol that produces the type of precise, tailored results that help us in our development processes, but can also help everyday riders who use Notio to pinpoint aero advantage in their personal setup. For both cases – Argon 18 in our development benchmarking, and regular riders in their own testing with Notio - we have to focus on consistency and producing results that are replicable, just like in any scientific or technical process. This means testing isn’t just about getting numbers – it’s about the accuracy of the test, and having the correct protocol to be able to measure small, incremental changes.
One of the major benefits of developing our in-house performance testing protocol with Notio is that we have access to results quickly, which can be seen and analyzed almost in real time, something that is essential to an rapid iterative design process. This means we can view results from test runs, and quickly see how design iterations can affect performance – and then go back to our design and manufacturing process and apply these learnings. We can also identify outliers and possible errors in our results right away, and can quickly correct things like rider position or consistency in components to be sure our results are accurate and actionable.
Using Notio, this protocol involves three different test environments, which each help us address a different set of variables, or help answer a different question: wind tunnel, real-world, and indoor track testing. Each presents its own set of challenges to measurement as well. In a wind tunnel, we can change wind speed and yaw as well as control the rider's position precisely, but the rider does not pedal or exert effort, so does not move on the bike as would be the case in a regular riding environment. On the track, the rider does move naturally on the bike, but there is no yaw measurement. Outside, we have all of the ‘real’ riding conditions and rider movement on the bike, but there is a challenge around consistent measurements because of changing wind, terrain, and rider position.
Notio and Argon 18’s benchmarking protocol: building replicable results
Recently we used this testing process to benchmark several bikes in our Tri/TT range: the E-117 Disc, E-118 and E-119 Tri+. The main goals of these tests were to compare the different TT bikes head-to-head. Because all of the models perform very well from an aerodynamic perspective, the differences in aero performance are very small compared to the overall performance of the rider and bike. That means we are looking for very small incremental advantages or differences between the models, which is where having a precise testing protocol is essential.
For the Notio team, developing this protocol allows for the opportunity to apply the knowledge acquired from working with pro teams, like the Hubb-Wattbike track team, and put it toward Argon 18’s bikes. Developing a testing process allows the team to check the repeatability among different points of measure, and also provides valuable input to refine how Notio displays results, and how the team can assist Notio users in getting the most valuable data out of the device based on the way that data is captured.
In each of our test environments, it’s important to calibrate the data in the same manner, so that our CdA results have a consistent baseline. What we do is use a sphere – a shape that has a known CdA value (verified in the wind tunnel) - and test with and without the sphere to see if we are able to measure the difference with Notio. This sets our baseline data for the testing process.
In the Wind Tunnel
One of the major benefits of wind tunnel testing is the ability to control variables. In the wind tunnel a controlled air flow with known velocity is applied to the rider, and load sensors are used to measure the force applied by the air on the rider.
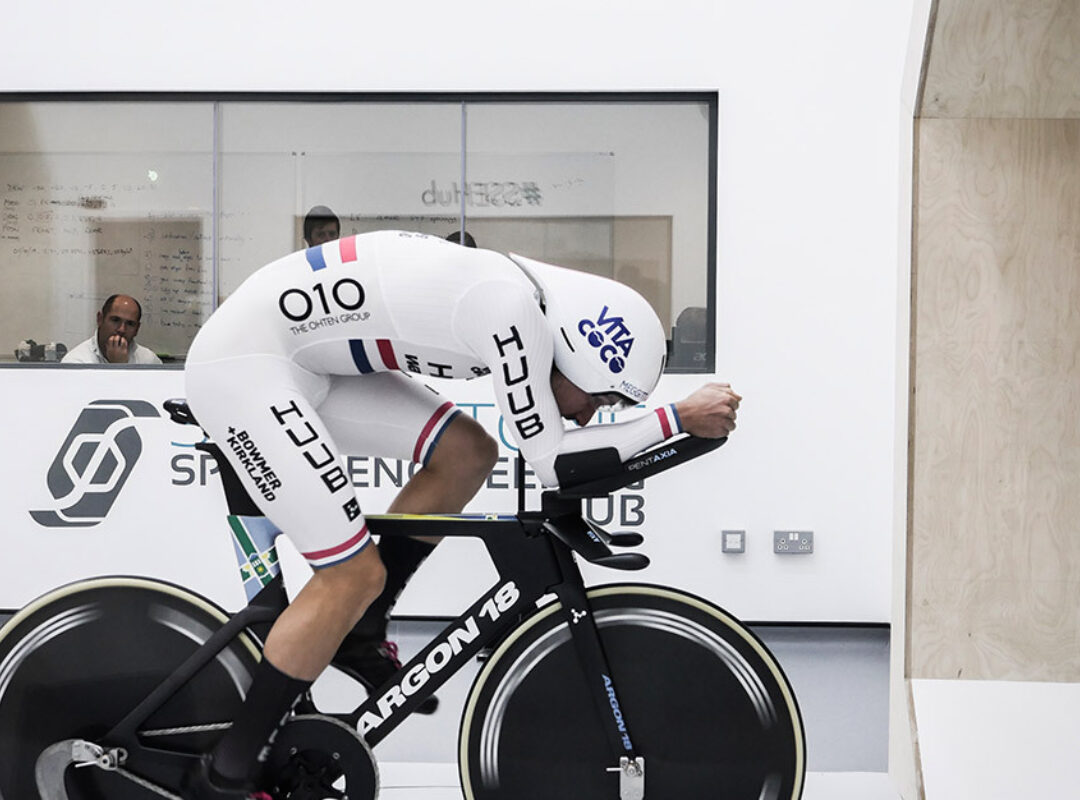
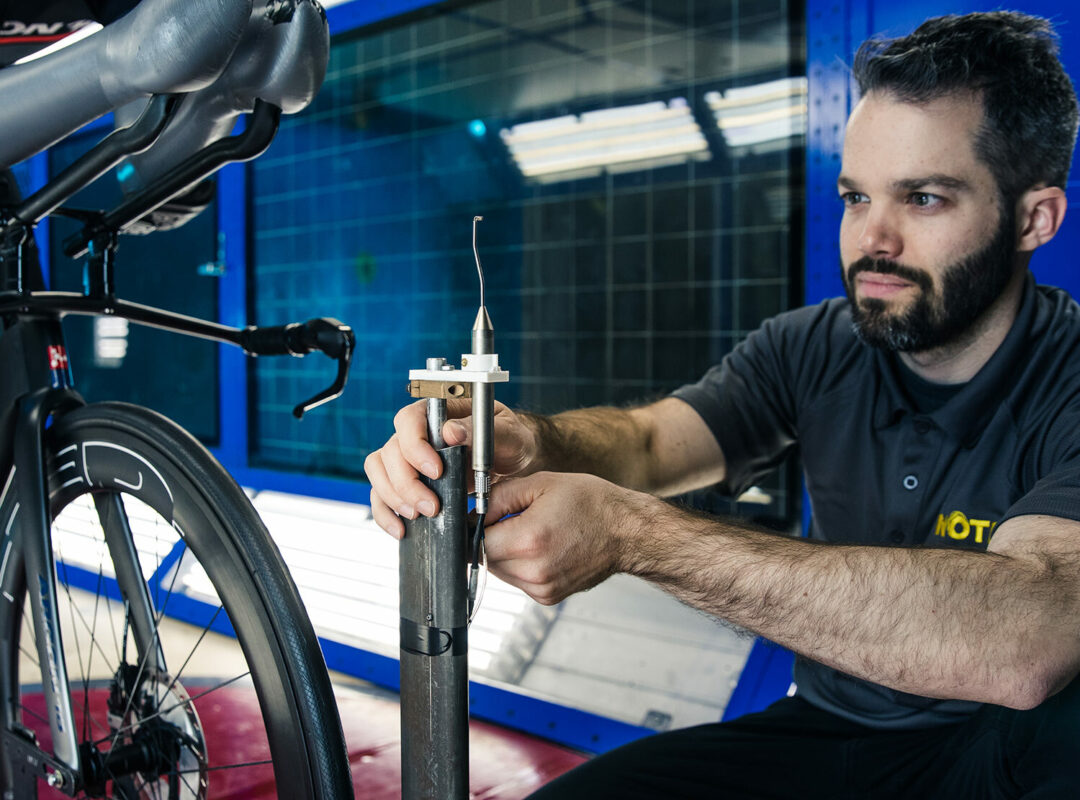
A real rider can be used during wind tunnel tests, however, it is difficult for a real person to keep exactly the same position between several tests. This means we would introduce variability, which makes small variations in measurements coming from the frame very difficult to evaluate. Therefore, a mannequin is often used. When we want to be sure we are collaborating our findings by testing the effect of the entire system – bike and rider – we can add outdoor, real-world testing into the mix.
Real-World Riding: Outdoor Testing
Outdoor, real-world testing is essential part of our protocol because this is where the conditions are, well, real. This is also the situation that most Notio users will be using to find their own aero advantage, as the average rider isn’t about to book time in a wind tunnel!
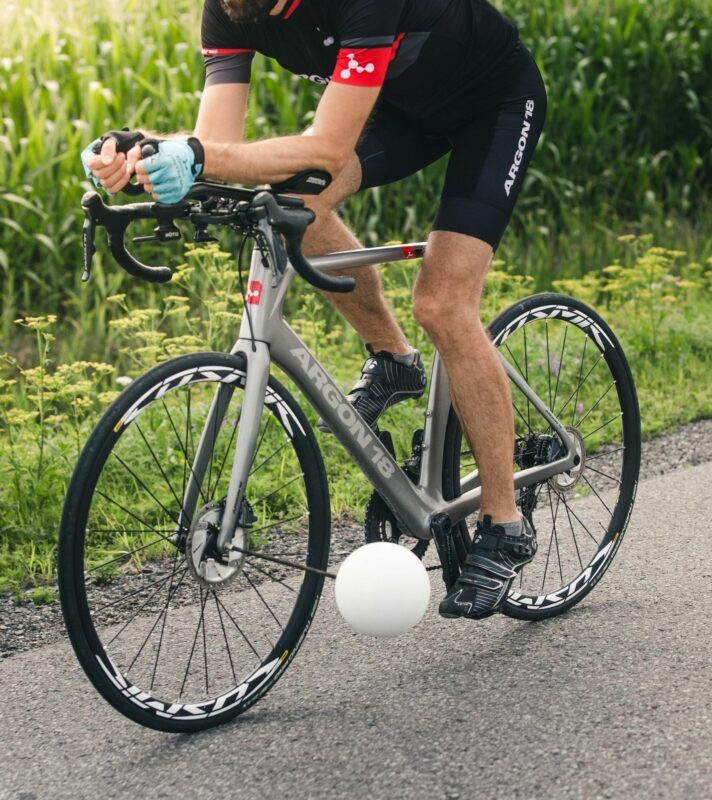
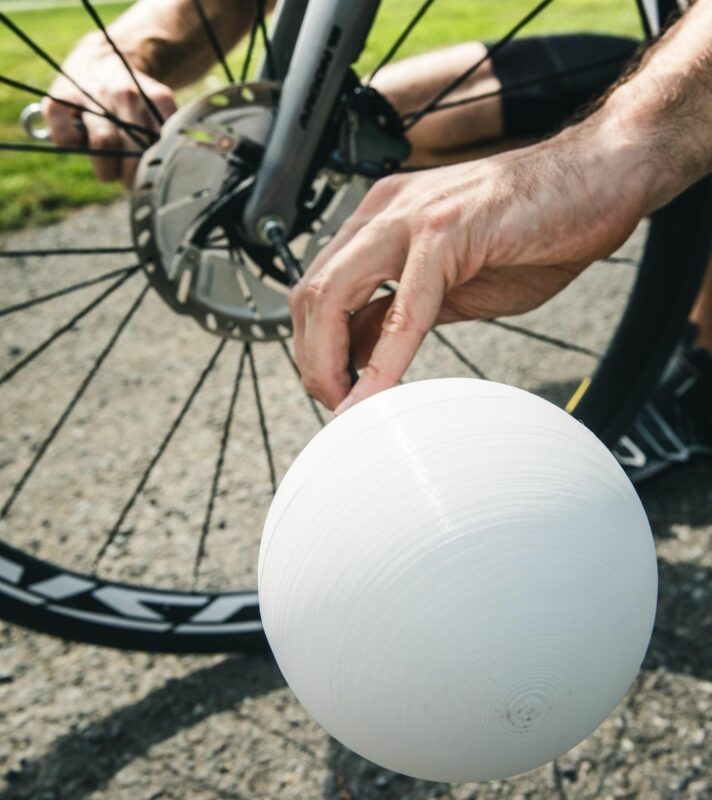
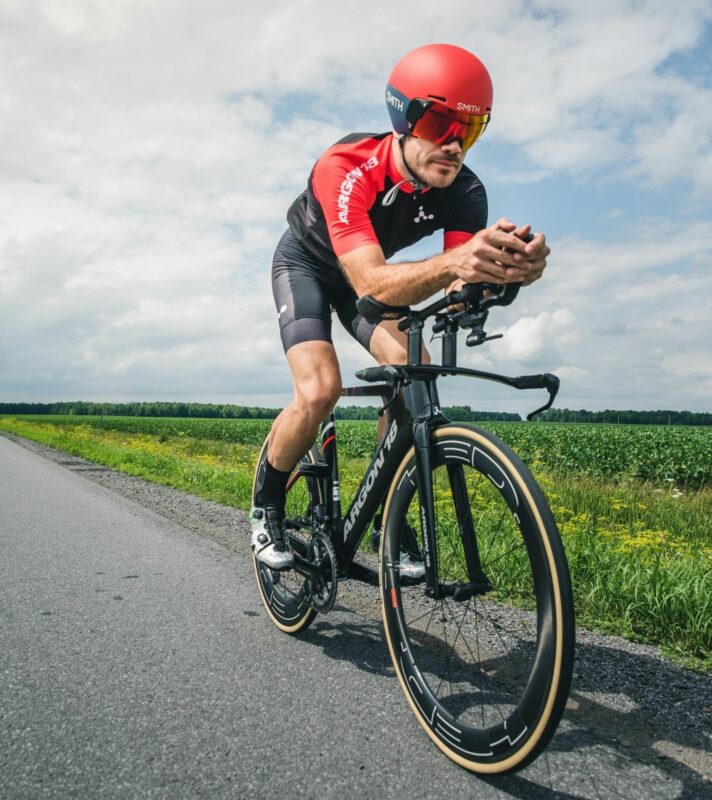
On the Track
At the indoor velodrome we also have a controlled environment, to a certain extent: no wind, a smooth surface, a predicable speed for the rider to maintain. Much like in the wind tunnel, this removes many of the unknowns or variables. In all test environments, including the track, the rider has to be very careful to be sure the same position is used and same speed maintained throughout the duration of the test, so that results are accurate. That means the rider choice is important, as that person must be very aware of their position and how their adjustments affect test results. Of course, people are not machines, and it is not possible to keep precisely the same speed during all the tests – either on the track or on the road. Notio takes this into account.
Our test rider, Argon 18 Lead Composites Engineer Joffrey Renaud, had to carefully match his position on all test bikes and maintain a steady speed of 41km/h over the course of 648 laps!
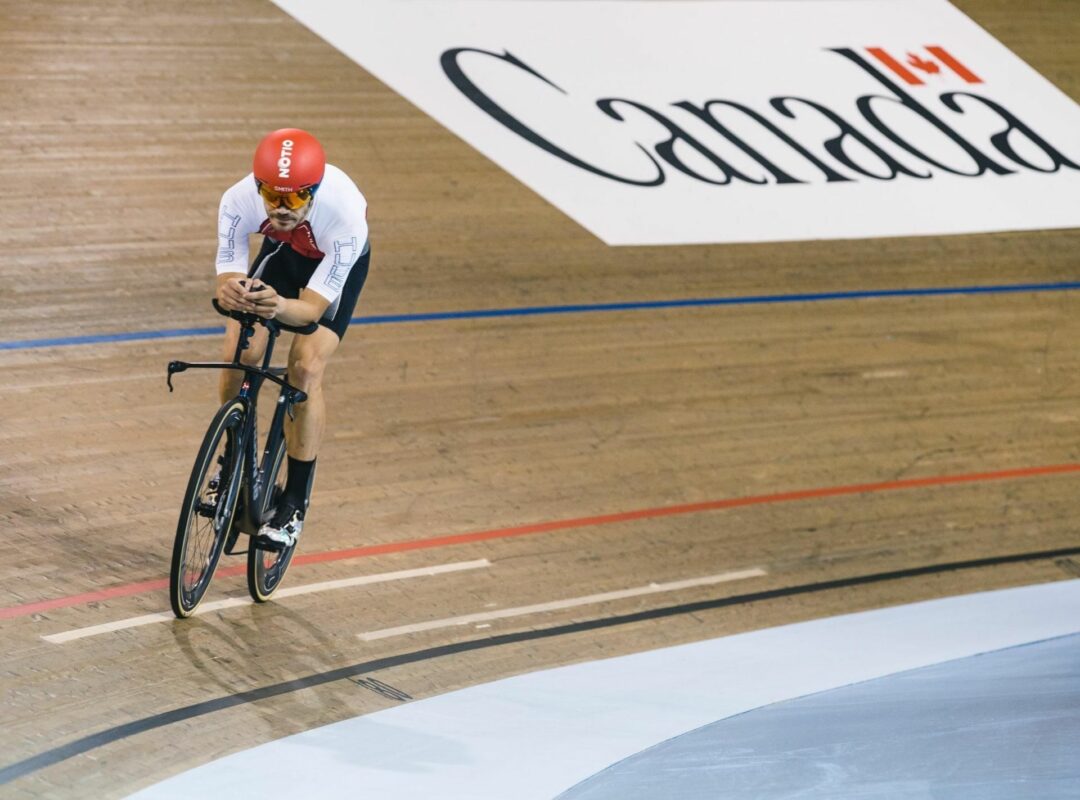
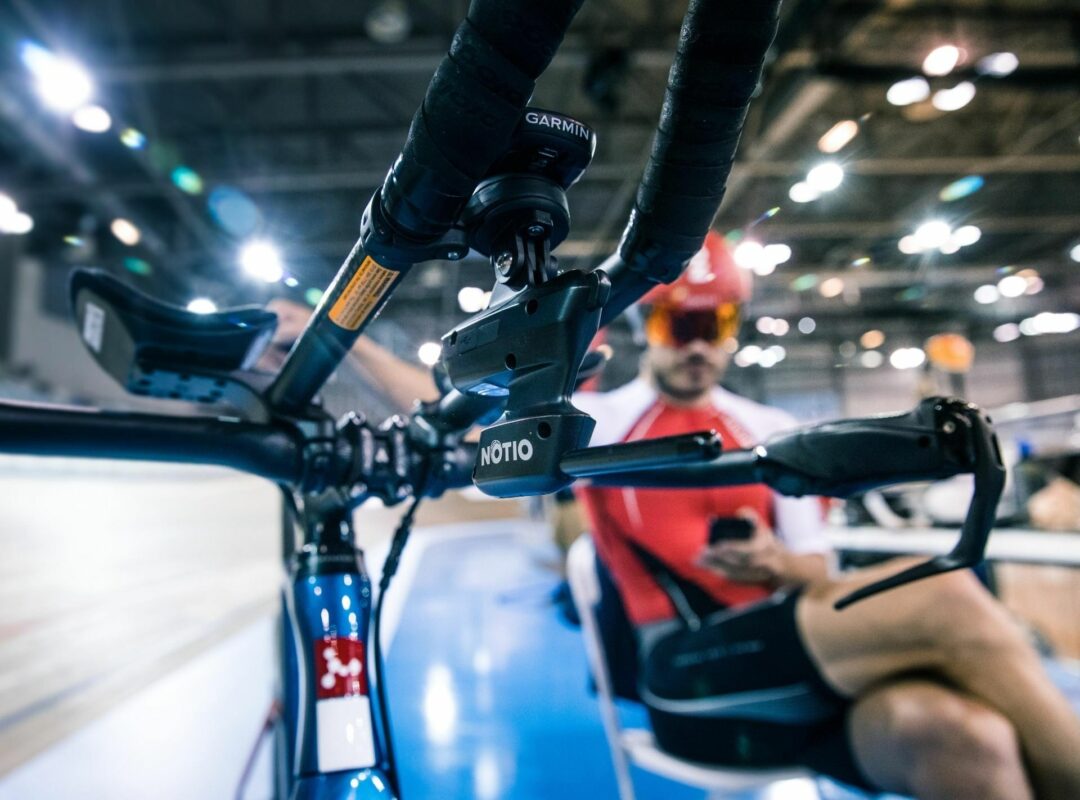